Introduction
Sommaire
Cela fait quelques années que je cherchais une génératrice adaptée aux caractéristiques de ma turbine (200W@1500 tr/min) mais je n’ai jamais trouvé le matériel adéquat.
Le meilleur rendement obtenu s’avère être le moteur de machine à laver utilisé en tant que dynamo que j’utilise depuis le début de l’aventure.
J’ai donc décidé de transformer un moteur asynchrone triphasé en génératrice synchrone à aimant permanent.
Pour concrétiser cette idée j’ai dessiné un nouveau rotor dimensionnellement identique à l’ancien, mais structurellement différent afin d’y loger des aimants en périphérie. J’ai ensuite imprimé ce nouveau rotor en ABS, inséré des aimants et expérimenté la nouvelle machine devenue génératrice synchrone.
La base à transformer : Moteur asynchrone triphasé
Mon choix s’est porté sur un moteur asynchrone triphasé dit à cage décureuil.
Le prix de ce type de moteur est ultra compétitif et côté fiabilité seuls les roulements sont à considérés comme pièces d’usure.
Un autre avantage à choisir ce type de moteur asynchrone normalisé est la possibilité de choisir une vitesse de rotation proche de ses besoins au travers des spécifications courantes, à savoir :
- 2 pôles = 3000 tr/min
- 4 pôles = 1500 tr/min
- 6 pôles = 1000 tr/min
- 8 pôles = 750 tr/min.
Le concept de la transformation
Processus en tant que moteur : on utilise une source électrique pour créer des courants statoriques qui génèrent un champ magnétique tournant dans le stator.
Le rotor est alors soumis aux variations de flux du champ magnétique, une force électromotrice apparait et crée des courants rotoriques qui génère le couple qui met en mouvement le rotor.
Processus en tant que génératrice : c’est l’inverse, on génère un champ magnétique tournant à l’aide des aimants placés sur le rotor, ce champ magnétique tournant induit à son tour des courant dans les bobines du stator …
La génératrice devient alors « synchrone » car sa fréquence est proportionnelle à la vitesse de rotation du rotor.
Note : on peut calculer la fréquence statorique avec la relation suivante :
V : Vitesse de rotation [tr/min]
P: Nombre de paire de pôles [-]
Les caractéristiques du moteur asynchrone choisi
Le stator est constitué d’un cylindre ferromagnétique entaillé d’encoches permettant d’y loger les bobinages. Ce cylindre est constitué d’un empilement de plaques de tôles feuilletées afin de limiter les courants de Foucault.
Le stator comporte 24 encoches, soit :
- 12 bobines au total
- 4 bobines par phase.
- Pas polaire : 6 encoches sous un pôle
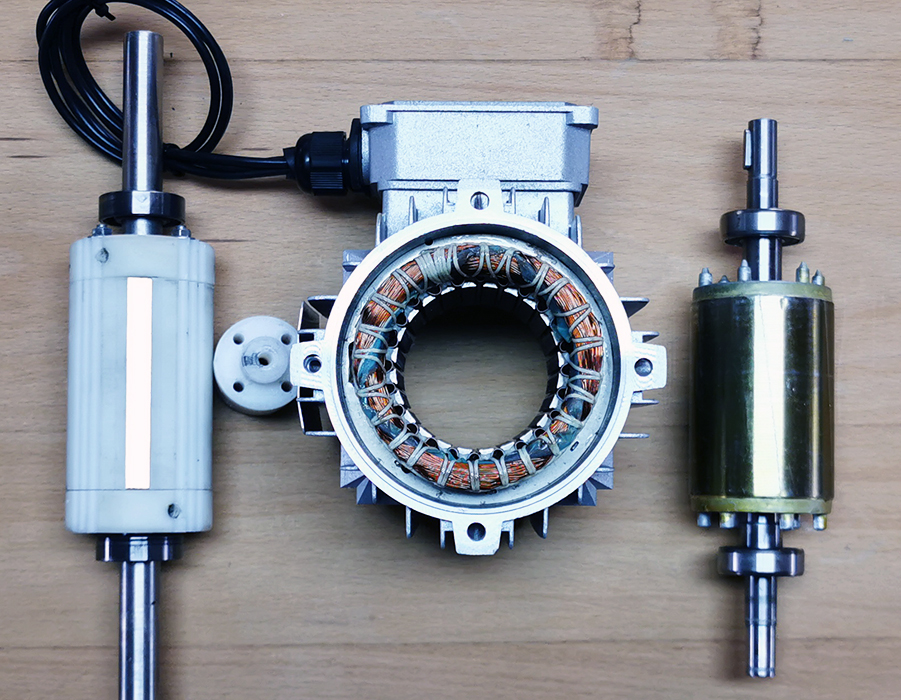
Le rotor à cage décureuil est constitué de tôles ferromagnétiques et de barres conductrices régulièrement réparties à la périphérie du rotor. Les barres sont reliées entre elles par deux anneaux de court-circuit. Les tôles ferromagnétiques servent à guider les lignes de champ tandis que les barres accueillent les courants induits.
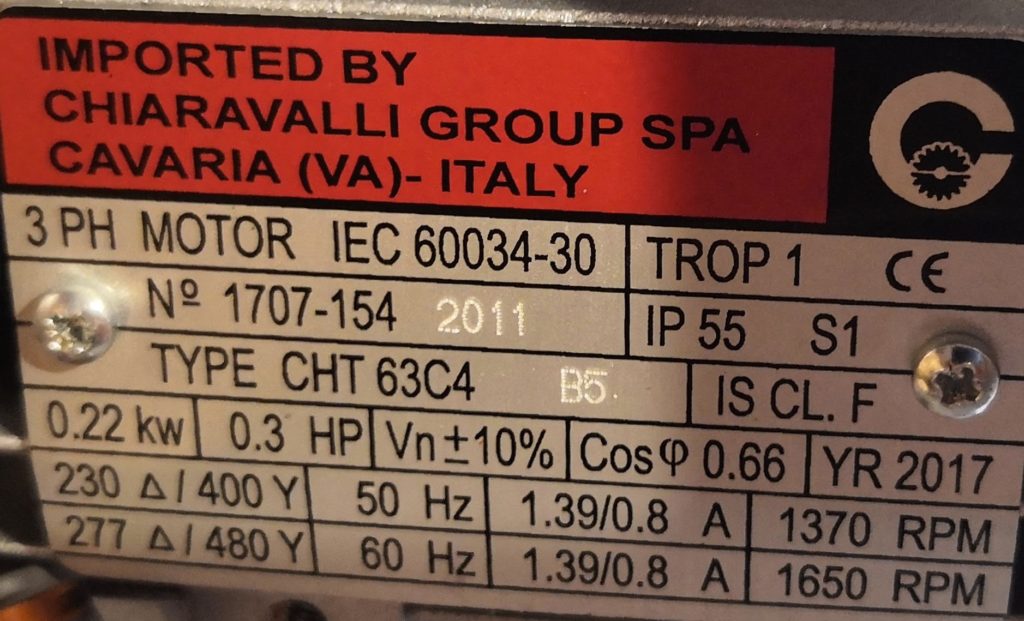
La vitesse de rotation à l’arbre devant idéalement se situer aux alentours de 1500 tr/min et sa puissance théorique étant de 200 Watts, j’ai naturellement choisi un moteur asynchrone triphasé normalisé se rapprochant le plus possible des caractéristiques souhaités.
Visant une puissance théorique de 200 W, j’ai choisi un moteur « plaqué » 220 W.
La vitesse de rotation devant se situer aux alentour de 1500 tr/min, j’ai choisi un rotor à 4 pôles.
J’ai volontairement « surclassé » le moteur choisi car n’oublions pas qu’il sera détourné sa fonction initiale et que le rendement en sera forcément affecté.
Visant une puissance théorique de 200 W, j’ai choisi un moteur « plaqué » 220 W.
Caractéristiques détaillées
- 4 pôles
- 1500 tr/min
- 220W
- Hauteur d’axe : 63 mm
- Câblage : étoile ou triangle
- 230△/400Y 1370rpm
- 277△/480Y 1650 rpm
Conception du rotor imprimé
J’ai dessiné un rotor d’un diamètre et d’ une longueur strictement identique au rotor initial afin qu’il puisse loger dans le stator. Le nouveau rotor comporte 2 paires de pôles soit 4 aimants formant les 4 pôles magnétiques.
La partie principale (en blanc sur l’image ci-dessous) acceuille les 4 aimants.
Les flasques, de couleur verte, interdisent la translation des aimants.
L’ensemble rotor/flasques est maintenu assemblé par l’intermédiaire de 4 goujons M4 traversants. Ces goujons devraient idéalement être en laiton afin de ne pas perturber les champs magnétiques produit par le rotor.
Télécharger le fichier STL du rotor
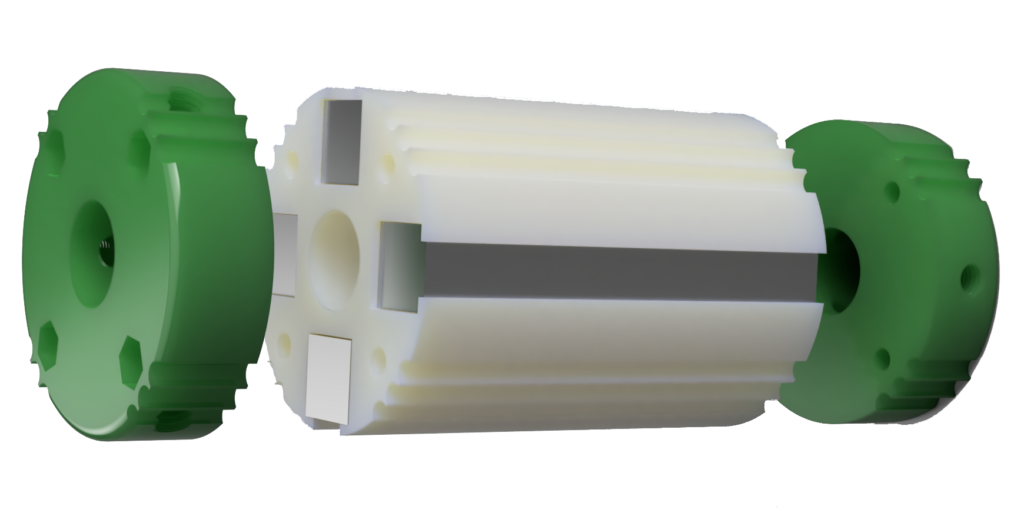
Afin de reproduire les 4 pôles magnétiques je vais utiliser 4 aimants disposés à 90° avec les polarités suivantes :
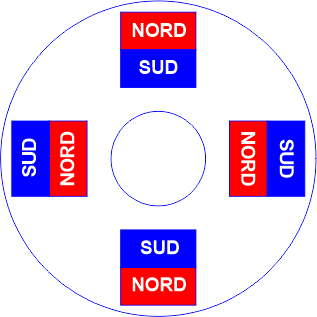
Les aimants sont des parallélépipèdes mesurant 3″ x 1/2″ (7,62 x 1,27 cm)
Material: NdFeB (néodyme, fer et bore)
Force : 34 kg
Poids : 92 gr
température de fonctionnement maximum : 80°C
Le site ou j’ai acheté les aimants : K&J Magnetics, Inc.
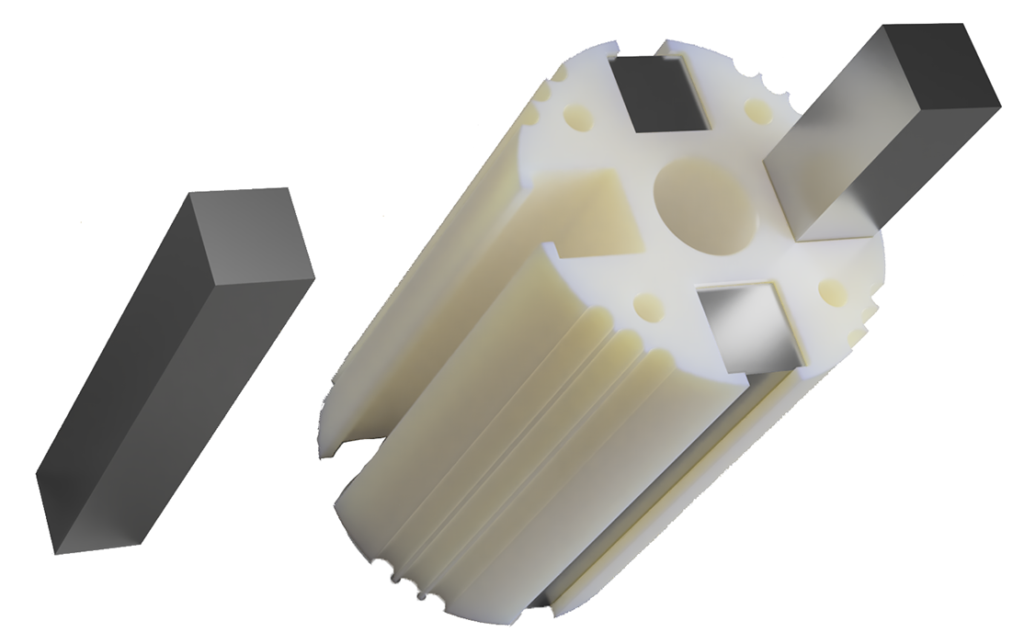
Dans l’images ci-dessus on peut voir les 4 encoches destinées à recevoir les aimants.
Les aimants n’étant pas vissés on note la présence d’une « rainure » empêchant l’ejection radiale des aimants, cette caractéristique influe grandement sur la taille de l’entrefer et serait à éviter pour diminuer la distance entrefer.
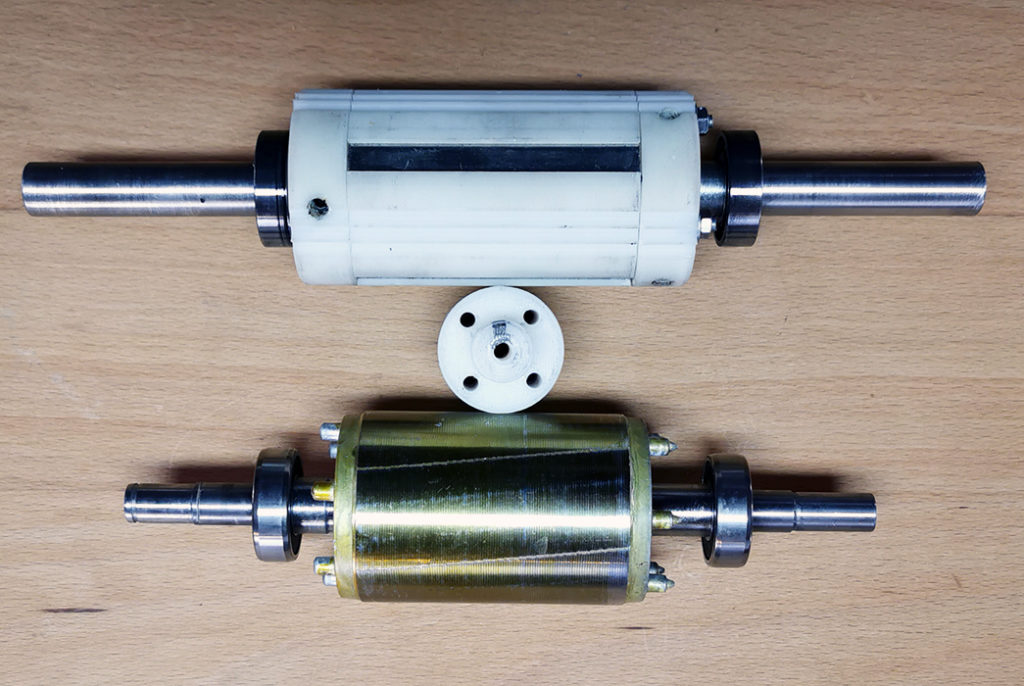
Sur la photo ci-dessus on peut voir le nouveau rotor imprimé en ABS avec les aimants, les deux flasques latérales (interdisant la translation des aimants sur l’axe), l’axe et les 2 roulements.
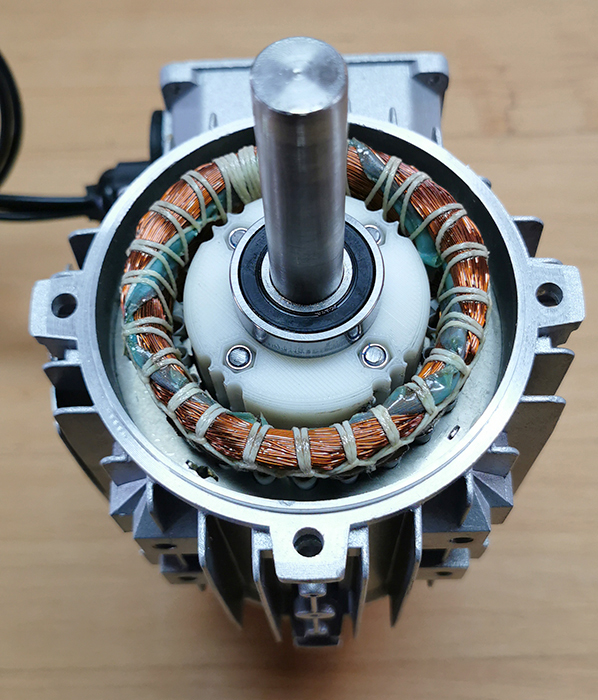
TESTS
A vide
Un petit test sans grande valeur mais qui se veut rassurant.
Comme on peut le voir dans la vidéo le nouveau rotor est pleinement fonctionnel, le générateur alimente sans problème une lampe LED de 3W@12V.
Le « cogging » est également très faible. Le cogging c’est la résistance que l’on ressent lorsqu’on tourne l’arbre d’un générateur à aimant permanent à vide, ce couple « résistant » est produit par les aimants du rotor.
Ce phénomène est caractéristique des générateurs à aimants permanents à faible vitesse de rotation. On retrouve également ce phénoméne au niveau des moteurs pas à pas (stepper) ou l’on peut même sentir le « pas ».
Ce couple résistant augmente quand on court-circuite les phases d’un PMG.
En charge sur turbine
Les mesures sont effectuées entre phase, les charges connectées utilisées sont des ampoules à incandescence d’une puissance de 100 Watts, au nombre de 3, une ampoule entre chaque phase. D’un point de vue physique les ampoules à filament sont des charges quasiment linéaires.
Résultats
Gains
Les résultats sont surprenants, la génératrice produit 180 Watts, le gain est de 50% par rapport au moteur de machine à laver que j’utilisais jusqu’alors (120 Watts).
Je précise cependant que cette puissance de 180 Watts obtenue n’est pas la puissance directement exploitable par mon installation.
Le moteur de machine à laver produisant directement du courant continu, ce dernier est exploité tel quel par le régulateur de charge, sans aucune modification.
En revance la nouvelle génératrice produisant un courant alternatif triphasé il sera impératif de redresser le signal et d’abaisser la tension (à cause de la tension maximum admissible par le régulateur), cela aura pour effet d’induire des pertes mais cette partie fera l’objet d’un prochain article.
Rapport Tension/Puissance
Le tableau ci-dessous résume les tensions et puissances obtenues en fonction du couplage (étoile ou triangle) et de la vistesse de rotation de la génératrice.
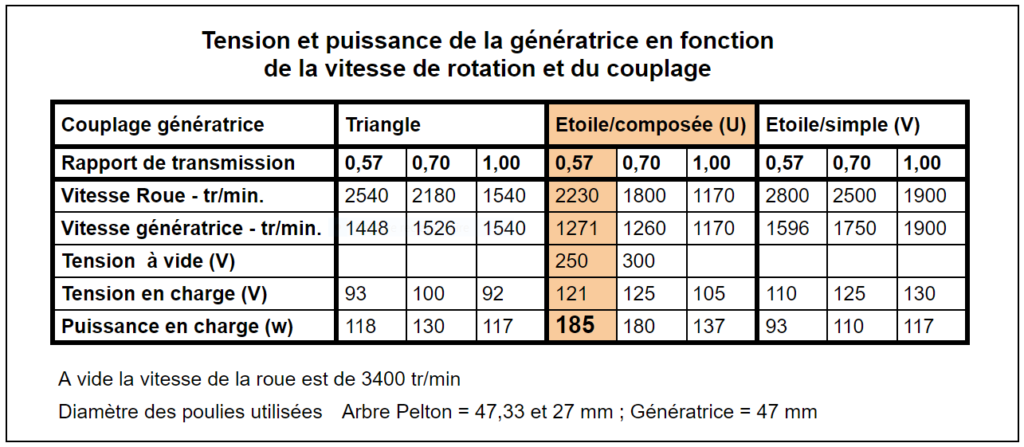
On constate que le meilleur résultat est obtenu lorsque la génératrice est couplée en étoile.
On notera également qu’indépendement du couplage le rapport de transmission à une influence sur le rendement de la génératrice.
Vitesse de rotation
Prenons l’exemple du couplage en étoile (colonne orange) :
Avec un rapport de transmission de 1, on observe qu’on perd 25% de puissance par rapport au rapport de 0,57.
Cela s’explique en partie par le fait qu’avec un rapport de transmission de 1 le couple roue/génératrice n’est pas dans sa plage de fonctionnement optimum, de 3400 tr/min à vide la vitesse s’éffondre aux alentours de 1170 tr/min.
En revanche, avec un rapport de transmission de 0,57, on gagne 25 % de puissance, ce qui peut en partie s’expliquer en partie par :
- La diminution de la vitesse de rotation de la génératrice (de 2230 à 1271 tr/min)
- L’augmention du couple côté génératrice (dû à la diminution de la vitesse)
- La vitesse de rotation de la génératrice s’approche de sa conception initiale (1271 tr/min réel contre 1500 tr/min théorique)
Cette vitesse de rotation à également une incidence sur la fréquence du courant produit mais cela n’est pas dérangeant en soi car dans mon cas de figure le courant alternatif est converti en courant continu (à l’aide d’un pont de diode à double alternance).
Forme des sinusoides
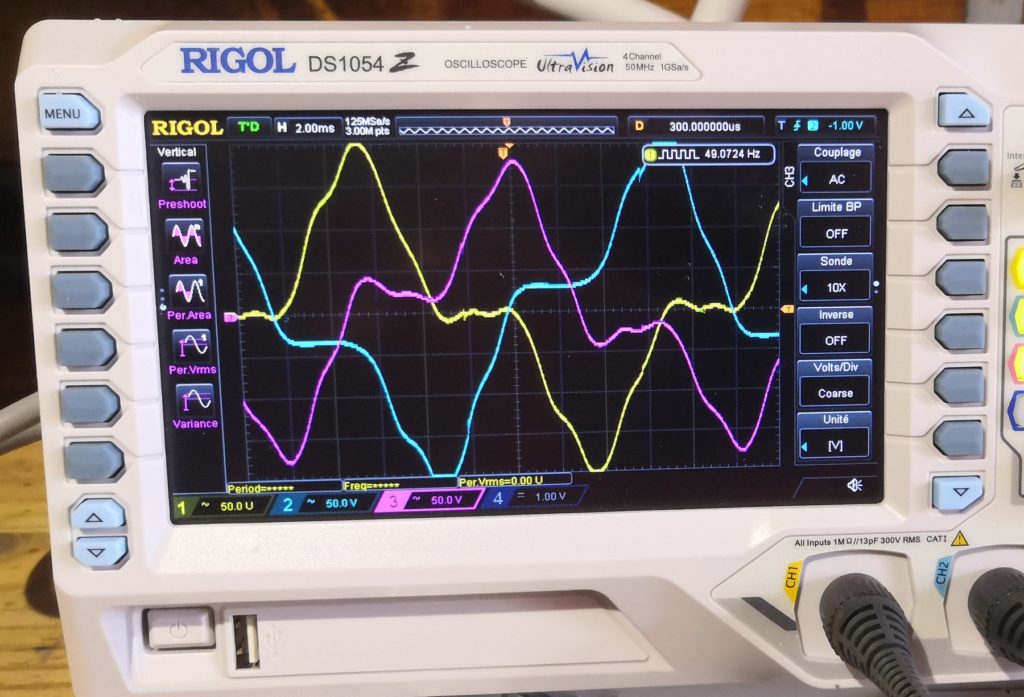
Amélioration
- Imprimé en ABS le rotor ne peut pas générer de circuit magnétique. Pour résoudre ce problème, on gagnerait à usiner un rotor en acier doux, ou usiner le rotor initial.
- Pour diminuer l’entrefer on pourrait utiliser des aimants en forme d’arc dont le rayon serait identique à celui du rotor initial. Ces aimants seraient vissés sur le rotor.
Bibliographie
- Magnétisation des machines tournantes : Université Paul Sabatier – Campus de Tarbes
- Initiation au bobinage par Gérard LABOBINE : inititiation au schema de bobinage
- Principes de réalisation des schémas de moteurs asynchrones : principes de base
- Machines asynchrones : Wikipédia
Salut Laurent. as tu pensé pour diminuer l’entrefer a enlever l’encoche de maintien des aimants , les mettre a fleur du rotor et les retenir avec un fil en fibre de verre enroulé sur le rotor puis enduit de résine? je dis ça car sur les servomoteurs que j’utilise , les aimants sont « sécurisés » de cette maniere
encore moi. que pensez vous qu’il se passe si je laisse le bobinage existant (pour moteur 4 poles 1500 trs/mn) mais que j’intègre 8 Aimants sur le rotor (4N. et 4S ) sachant que la vitesse sera de moitié (maxi ,750trs/mn )
Que sera le courant fourni s’il y en a un !!!!!
Merci de vos commentaires
Bonjour André,
La question que j’ai envie de vous poser c’est pourquoi vous ne modifiez pas directement une base de machine 4 paires de pôles – 750 tr/min.
Car c’est finalement une machine similaire que vous éssayez de faire en :
On peut déjà prévoir que vous allez retrouver une fréquence d’environ 50 Hz, c’est certain.
En revanche au niveau bobinage du stator cela risque de ne pas jouer, on attends votre retour d’experience ou qu’un utilsateur plus averti nous donne des explications rationelles.
Cela me semble cependant contre productif, à plus forte raison si vous songez à revoir les bobinages du stator !
Je vous invite à lire le post ci-dessus afin d’y voir un peu plus clair.
Cordialement
Rebonjour , je crois que je raconte de grosses betises concernant la modification d’un moteur actuellement 4 poles 1450trs/mn .Je rappelle mon projet : genetateur entrainé par une roue a aubes dont la vitesse de rotation ne devrai pas depasser 600 à 750 trs/mn , d’ou mon souhait de crer un generateur 8 , 10 ou 12 poles ‘ pour avoir une vitesse de rotation de 750 ;600 ou 500 trs/mn
Aussi je ne pense pas que multiplier le nombre d’aimants sur le rotor soit suffisant . Un modification du bobinage me semble indispensable . Mon moteur comporte 36 encoches et 6 bobines occupant chacune 6 encoches en serie 2 a 2 . bobine 1 : encoche 1,2,3 sens N et encoche 10 11 12 sens S en serie avec bobine 4 / encoche 17 18 19 sens N et encoche 28 29 30 sens S , bobine 2 : encoche 7 8 9 sens N et encoche 16 17 18 sens S en serie avec bobine 5 …Ect ……
Je ne sais pas comment modiifer le bobinage pour augmenter le nombre de poles compte tenu que je n’ai accés qu’aux entres sorties des 6 bobines
Qu’en pensez vous ?
Merci de votre analyse car vous semblez bien connaitre l’electrotechnique
Salutations
je reviens sur mon rotor modifie de moteur 1.1kw. compte tenu de la roue à aube qui entraînera le générateur j’envisage d’installer 12 lignes d’aimants( 6N et 6S ) pour une vitesse de rotation de l’ordre de 500 trs/mn. comment définir les aimants pour une puissance optimale ? quant a l’usinage du rotor d’origine je pense quand même ajouter des tirants pour tenir l’empilage de tôles. merci de vos conseils. Andre
Bonjour Laurent, avez vous fait évoluer votre rotor et fait d’autres essais ?
Pensez vous possible d’usiner le rotor d’origine pour loger les aimants car c’est un empilage de « rondelles », pas certain que le rotor se « tienne ».
Christophe
Bonjour Christophe,
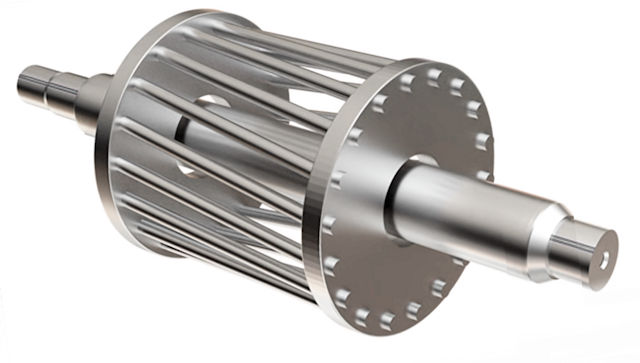
Je pense qu’il est tout à fait possible d’usiner le rotor intitial pour créer les encoches destinées à recevoir les aimants, la tenue du rotor est une bonne question mais je pense qu’un rotor à cage d’écureuil ne se déformera pas car les multiples tôles laminées constituant le noyau sonts traversées par de barres conductrices réunies par deux couronnes. (Photo ci-dessous)
De mon côté je verrais les 2 évolutions suivantes afin d’améliorer le prototype de rotor réalisé en ABS:
Je prépare également un article expliquant comment transformer un moteur asynchrone triphasé en génératrice asynchrone en ajoutant des condensateurs entre phases en prenons comme exemple l’expérimentation de mon ami Cristof.
Cordialement,
bonjour. j’envisage de transformer un moteur asynchrone triphasé en générateur come vous l’avez fait. Tailler dans le rotor me paraît difficile car les barres de jonction de la cage d’écureuil ne sont pas sur des génératrices du cylindre .la réalisation des rainures va couper ces barres et les tôles ne seront plus tenues. je pense qu’il vaut mieux faire un rotor en acier plein ,cela me paraît plus simple. quant aux aimants comment faut il les dimensionner ? . j’envisage de mettre 12 aimants pour une rotation de l’ordre de 500trs/mn . est ce que je me trompe ?. le rotor a un diamètre de 90 long 90 . cela limite les dimensions des aimants. merci de votre analyse
Bonjour André,
Je pense que c’est tout à fait possible : voir le post du 13 décembre 2024
Cordialement,
Laurent
Bonjour et merci pour ce super site, je souhaiterais avoir de l’aide pour le choix d’aimants pour la transformation d’un moteur triphasé en générateur. J’ai un potentiel hydraulique de 500W et j’ai récupéré un moteur triphasé de 370W, 4 Pôles 1500 tr/min. J’ai compté 12 bobines donc 4 bobines par phase. Le générateur sera connecté à 3 résistances de 100W pour chauffer de l’eau. N’ayant pas d’exigence sur la fréquence, je me demandais si il ne serait pas intéressant de faire un rotor à 8 pôles pour améliorer le rendement et diminuer la puissance de l’aimant. Pouvez vous me dire comment vous êtes arriver à choisir des aimants de 34 Kg ?
Merci d’avance
Bonjour,
J’ai choisi les aimants en fonction des contraintes dimensionnelles imposées par le rotor, point de calculs savants ici.
Autrement dit j’ai choisi des aimants existants sur le marché qui pouvait être dimensionnellement insérés dans le rotor.
Ceci pourrait être optimisé en faisant fabriquer des amants sur mesure, à savoir de forme arquée, afin d’épouser parfaitement le diamètre du rotor et diminuer ainsi l’entre fer.
Cordialement,
Laurent
Bonjour, Super votre site pour degrossir un projet de turbine pelton
Mon interrogation porte sur la generatrice à partir d’un moteur ..Je pense avoir la puissance pour entrainer un moteur asynchrone de 1.1kw
Questions :
Ou puis je trouver les barreaux magnetiques
Peut on usiner directement le rotor
Quel circuit electrique dois je creer, pour pouvoir alimenter un convecteur ( type grille pain)
merci de votre retour
Bonjour ,Merci pour votre site qui permet de bien dégrossir un projet de turbine
Pour ma part , je dispose d’un ruisseau sur lequel je dois pouvoir prélever environ 10 l/sec amenés dans un tuyau de diam70 sur une hauteur de 20m jusqu’à la turbine . je dois pouvoir en tirer 1100W
Mon interrogation se porte sur le generateur a utiliser . Le plus simple pour moi serai de partir d’un moteur asynchrone triphasé de 1.1Kw avec rotot modifié tel que vous l’avez presenté . La vitesse de rotation devrai tourner aux environs de 2115 trs/mn en prenant en compte 20% de perte de charge avec roue diam actif 160
1- a quel vitesse dois je faire tourner le moteur 1500 trs/mn ?
2: ou peut on trover les barreaux magnetiques
3 : quel circuit electrique faut il crer pour utiliser la puissance générée par le moteur soit directement sur un convecteur type grille pain , soit re-injecter sur reseau
Merci de votre réponse
Bonjour André,
Pour ma part j’ai trouvé les aimants ici :
K&J Magnetics, Inc.
On devrait usiner le rotor directement pour augmenter le champ magnétique.
Avec ce type de génératrice vous allez générer un courant alternatif triphasé, a vous de le transformer en fonction de vos besoins.
Cordialement,
Laurent
bonjour,un moteur asynchrone triphasé étoile de 2900 tr/mn, je voudrais le transformer en générateur en modifiant le rotor.
pour ce fait, combien de pôle aimant puis je utiliser pour garder la même vitesse ?
Bonjour,
2900 tr/min c’est typiquement la vitesse de rotation d’un rotor comportant 2 pôles magnétiques alimenté par un courant alternatif 50 Hz.
Donc si tu veux créer un courant alternatif avec une féquence s’approchant de 50 Hz en tournant à 2900 tr/min il faut ajouter 2 pôles magnétiques à ton rotor, soit 2 aimants diamétralement opposés en inversant leurs polarités afin que le stator voit passer un pôle Nord et un pôle sud lors d’une rotation.
Si le rotor tourne moins vite cela va modifier la fréquence, que l’on peut calculer avec la relation : F (Hz) = V (tr-min) / 60 (min) * nombre de paire de pôles
Question bonus : quelle sera donc la fréquence d’un rotor comportant 4 paires de pôles tournant à 500 tr/min ?
Aussi le nombre usuel de paire de pôles est le suivant pour les moteurs les plus courant:
Cordialement,
Laurent